
360 Sanitary Bin
A modern sanitary bin for quick and clean servicing.
Client
Year
Brief
2013 - 2022
Woosh Washrooms
Develop a suite of sanitary bins for commercial environments that improve the efficiency of cleaning and maintenance. To deliver a successful range the solution needed to:
Minimise the need to recover and clean the base.
Take up minimal space in transit.
Offer a discrete waste solution.
Have update options to sensor or foot operated variations.
Stand out with a modern aesthetic.
Be customised for specific customers.
Outcome
Initially conceived, developed, and brought to manufacture a hand operated bin. After a successful period in market we developed additional systems to convert the original bin to being electronically sensor operated and foot pedal operated. These two optional upgrades mount to the existing bin.
These bins have been used within the Woosh ecosystem for many years and have proven to reduce service costs by improving efficiency, while drawing new customers with the modern aesthetic. The retrofit sensor operated mechanism has proven a highly reliable update, capturing further customers who did not a manually operated bin.
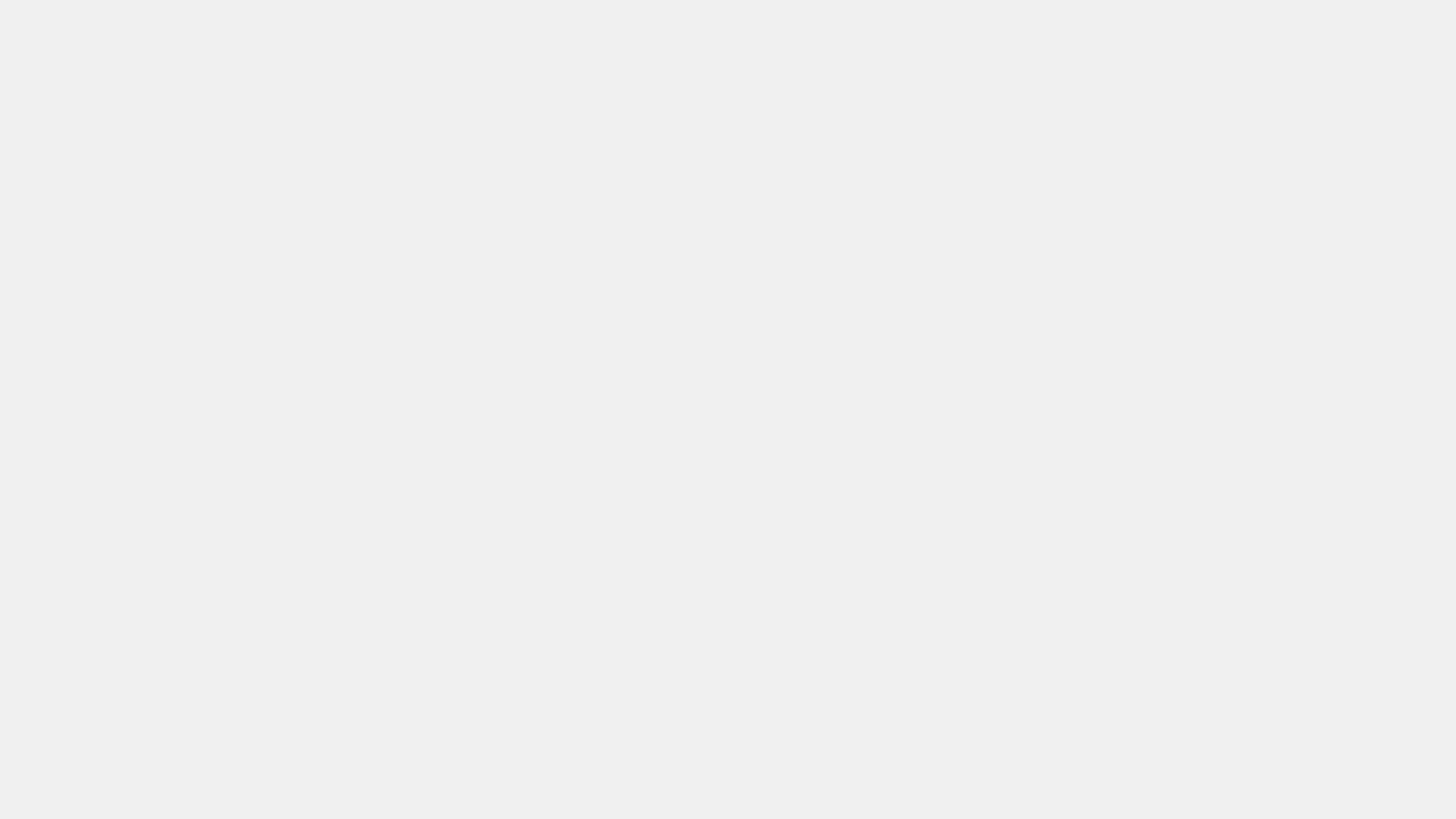
Key Design Features
A novel bag solution, attached directly to the lid, which minimises the need for regular transport and cleaning of the bin body.
Sleek tessellating form that reduces storage and transport volume.
Optional sensor and foot operated add-ons to eliminate allow touch-free use.
Weighted base to improve stability.
Wrapping and spraying options for customising the outside colour and patterns.
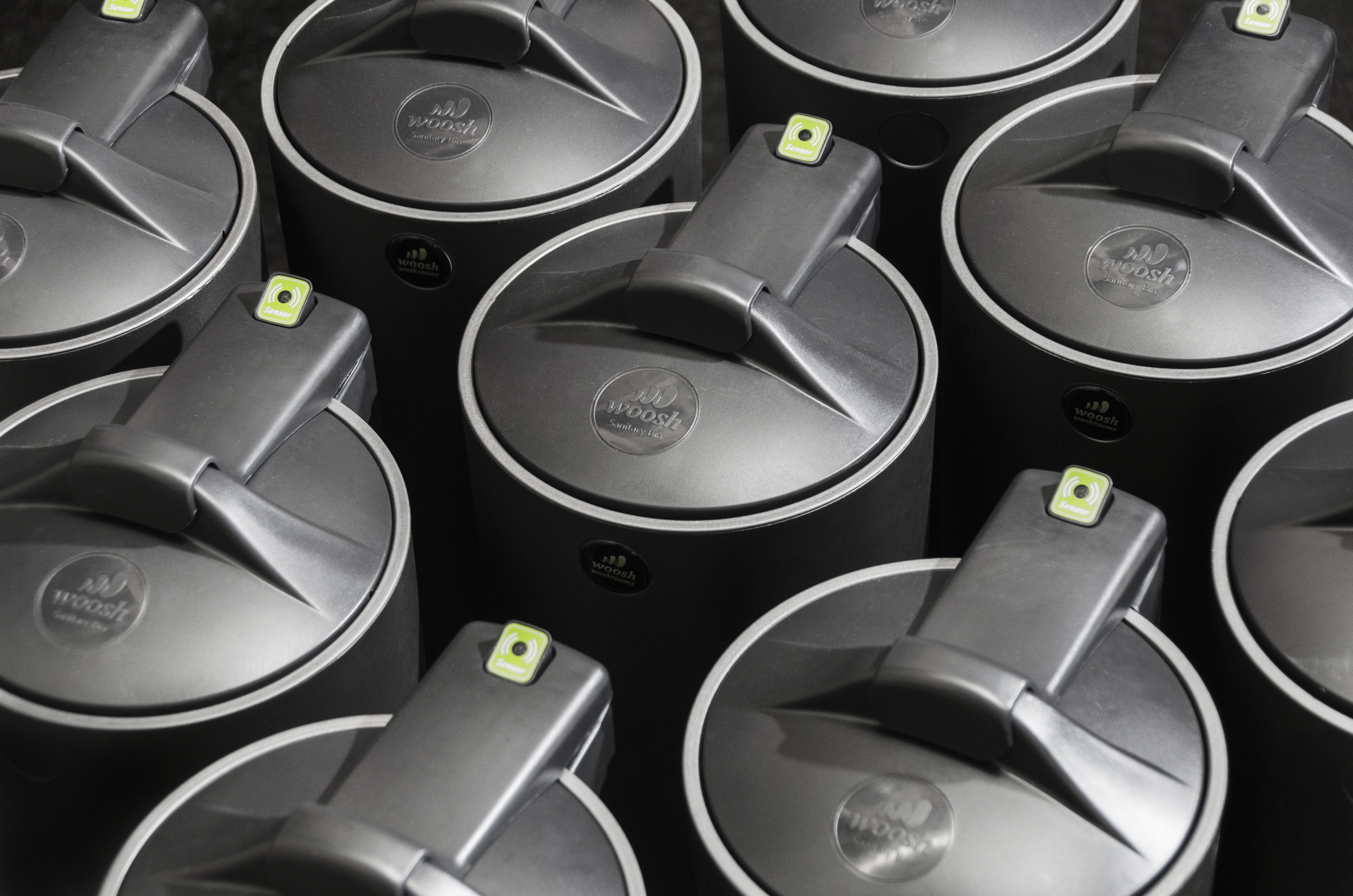
Improving Business Efficiency Through Considered Product Design
Woosh services public and commercial washrooms across Britain, which means that small inefficiencies can have a huge impact on customer retention and revenue. We listened to their frustrations to inspire design features which meant that less time was taken to install, maintain, and clean their sanitary bins across countless sites.
One key innovation was the patented lid, which we thermally welded to a custom bin bag. This means that sanitary waste was less likely to soil the bin base, reducing the number of bins which needed to return for cleaning and speeding up replacements.
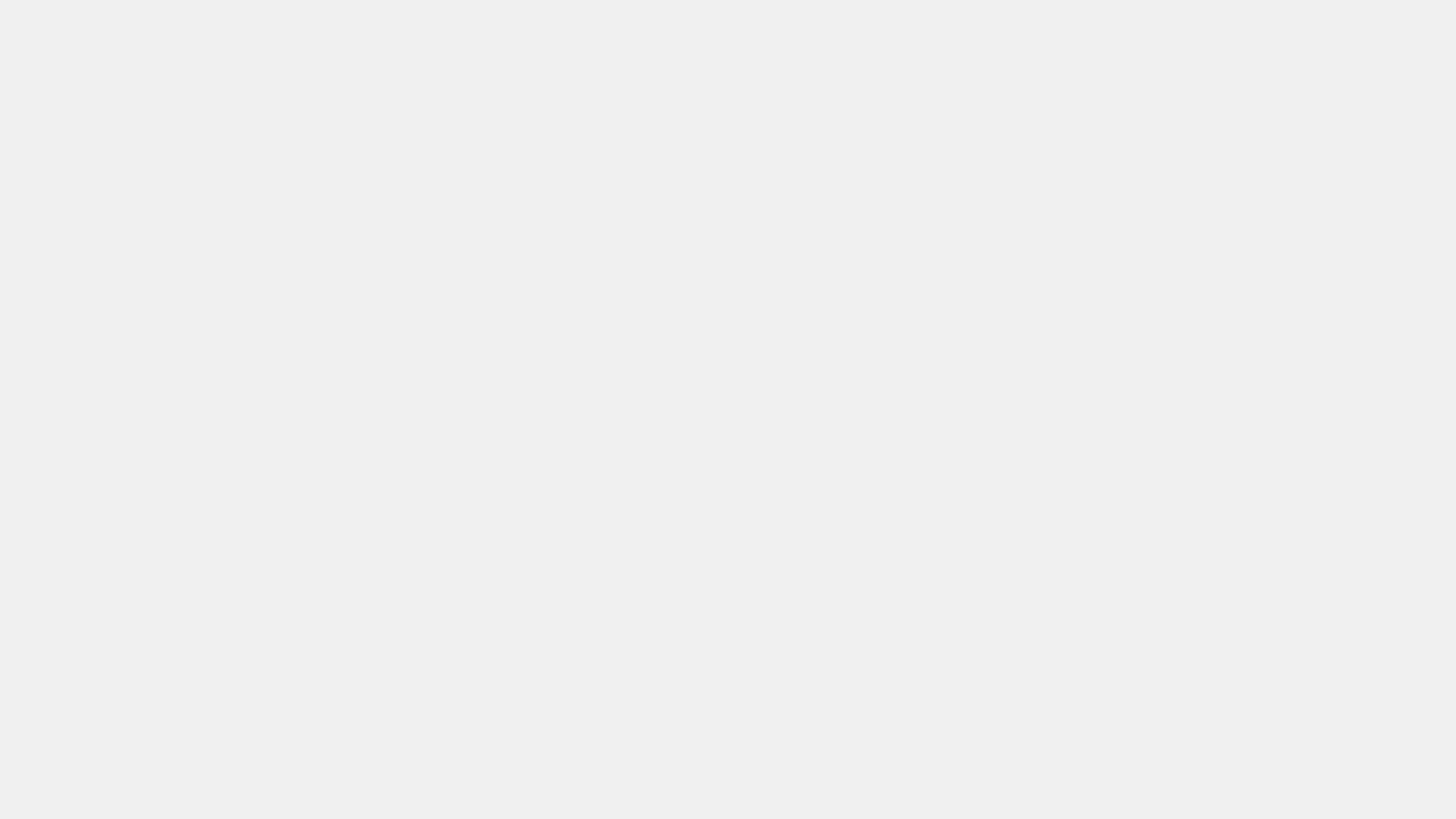
Engineered for Manufacture
We developed every part of this suite of bins through to production, which included engineering drawings and assembly instructions. Having worked alongside the chosen manufacturing partner to refine the designs, we supported the project to market, were many thousand have been operating reliably in a revolving service for many years.
The bin body and lid components were particularly challenging due to their scale. The large 550mm tall base boasts flat, gently curving, sides which would too easily show witness marks to internal features without considered engineering. Similarly, the lid with welded bin bag contains several complex features necessary to install and run in the base while being prone to warping.
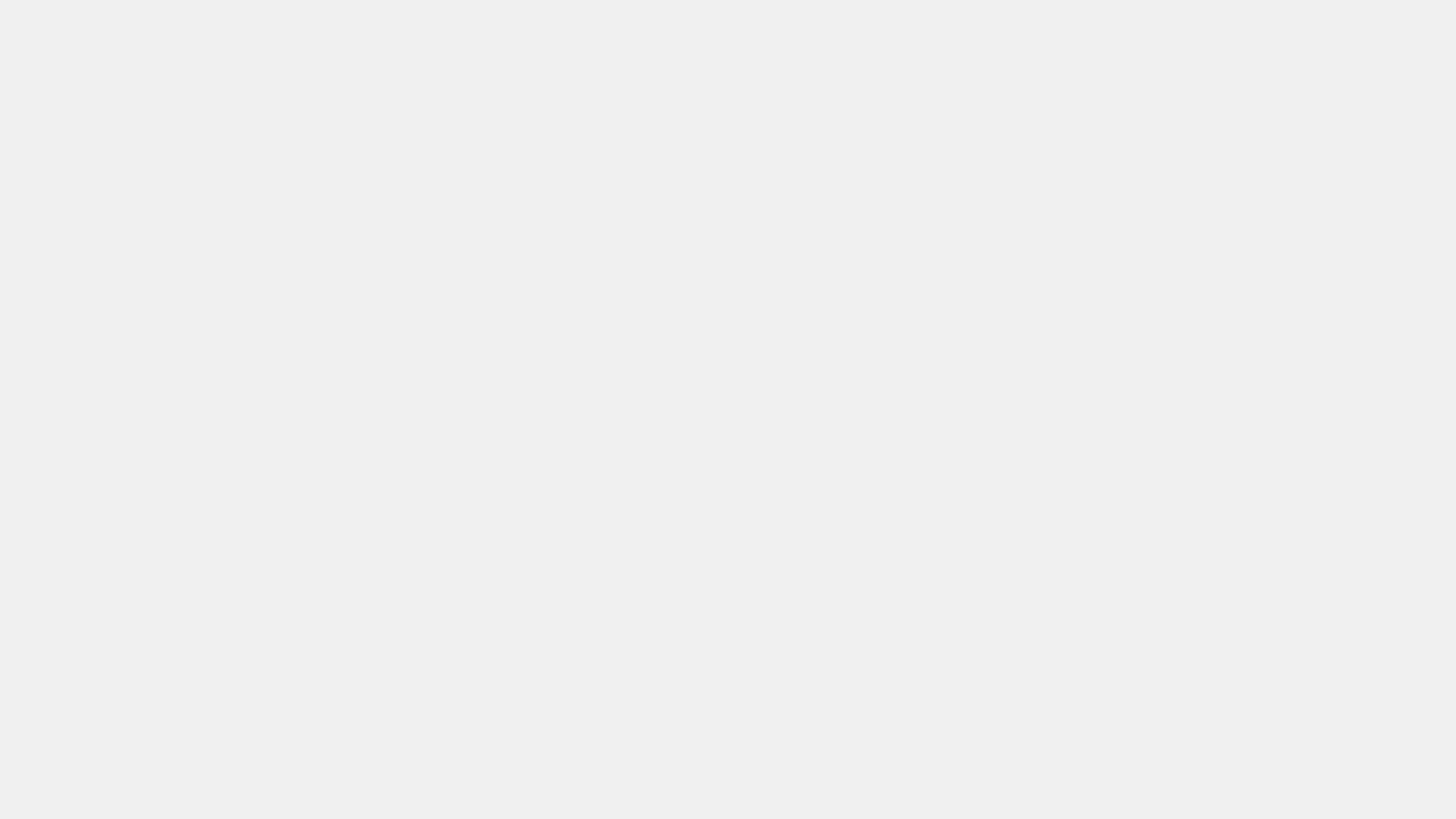
Reducing Complexity to Extend Product Life and Minimise Costs
A key driving factor in this project was simplicity. We took otherwise complicated mechanisms and reduced the number of parts while maintaining functionality. This served to reduce capital investment, assembly time, and unit price. Furthermore, this made for a more robust product which has a proven long life even when confronted with a challenging environment and careless users.
After delivering a functional prototype for the optional sensor system, we then undertook a redesign which saw us consolidate multiple parts and features into a single moulding. Alongside other similar changes, we were able to deliver the sensor system with just two moulded parts, an extrusion, and some choice 3D printed components. The outcome was a design with minimal tooling and assembly costs with very little to break during use.
Inhouse Prototyping to Test Mechanisms
Through development we produced numerous prototypes to test ideas and steer decisions. This was most notable during the design of the retrofit sensor and foot operated systems. We used our workshop to modify production bins with inhouse 3D printed components as well as externally sourced components.
The foot pedal went through several prototype iterations. Initially these were quick models to confirm fundamental geometry and function, however they evolved into high-quality, full-scale, mock-ups which communicated form while giving us a platform to test assembly and manufacturing features.
